Et dire que les anciens plaçaient le Mont Olympe sur le toit du monde !
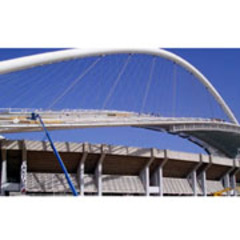
Ce "joyau de la couronne", comme on appelle la toiture du stade, flanqué de ses deux arcs gigantesques d'une portée de 304 m et qui culmine à une hauteur maximale de 80 m, est à même de devenir le fleuron des Jeux Olympiques de 2004. Chaque arc assure le soutien des câbles qui maintiennent en place les panneaux en polycarbonate de la toiture, avec un poids total de 17.000 tonnes et une surface de 10.000 mètres carrés pour abriter 75.000 spectateurs et athlètes.
L'élégante et majestueuse structure de verre et de métal de la toiture est recouverte d'un enduit spécial conçu pour refléter 60 pour cent de la lumière du soleil (caractéristique non négligeable l'été en Grèce). La spécificité du projet réside dans sa structure et son design architectural unique, la rénovation du stade se faisant parallèlement à la construction de la toiture et à l'érection des arcs.
Nouveaux segments de toiture construits hors du site olympique pour éviter
de gêner les travaux du stade.
La toiture – une structure en forme d'arcs bowstring doubles reliés
– a été assemblée à proximité du stadium.
Les arcs et la toiture ont été construits séparément
en deux segments et positionnés et assemblés à proximité
du Stade Olympique Oaka, à 70 mètres de part et d'autre du stade.
Ils ont été construits hors du site olympique pour éviter
de gêner les travaux du stade. Chaque arc est constitué d’un
tube d’acier de 3,5 mètres de diamètres avec une portée
de 304 mètres pour soutenir la nouvelle structure de pointe du toit.
Cette construction hors site a soulevé de nombreuses problématiques
dans l'esprit des ingénieurs dont : Comment déplacer et positionner
les deux segments d'une toiture pesant respectivement 8500 tonnes ?
La structure du toit en forme d'arc repose sur deux sabots maintenus par quatre patins de téflon. A l'origine, chaque segment de toiture devait être graduellement érigé au moyen de longs câbles toronnés, de mandrins et de vérins hydrauliques à faible course. Une telle technique impliquait le glissement des sabots sur de fines plaques en acier inoxydable soudées sur des rails spéciaux reposant sur d'imposantes poutres en acier.
Cependant, la simulation par ordinateur prédit l'émergence de problèmes potentiels résultant de l'utilisation de câbles pour hisser la toiture en position. D'après les calculs, en raison de l'élasticité des câbles, on s'exposait à un broutage résultant de la différence entre le coefficient de frottement statique et le coefficient de frottement dynamique du téflon et de l'acier inoxydable avec pour effet des accélérations relativement importantes et des arrêts brusques imposés à la structure pendant la phase de levage. Cette technique est jugée inacceptable par les concepteurs qui se tournent vers d'autres solutions.
Systèmes hydrauliques intégrés
Enerpac, spécialiste des systèmes hydrauliques intégrés,
des grands chantiers et expert en génie civil est consulté. Impliqué
dans des projets de construction de niveau mondial, Enerpac a également
pris part à la construction du viaduc de Millau (France), le plus haut
pont au monde, culminant à 364 mètres.
Pour la construction du stade d'Athènes, Enerpac propose l'utilisation
de vérins de traction à grande course alimentés par des
pompes hydrauliques contrôlées par automate programmable (PLC).
Leur utilisation en phase de levage progressif limite leur impact sur le design
actuel.
Les vérins de traction à double effet sont fixés aux sabots
dans un système de guidage coulissant permettant de hisser étape
par étape la toiture à arches jusqu’à sa position
finale.
Chaque sabot supportant la structure de toit en forme d'arc est accompagné
de quatre vérins de traction. Compte tenu que chaque arc est supporté
par deux sabots et que chaque sabot est maintenu par quatre patins, au total,
huit vérins hydrauliques sont nécessaires pour hisser et positionner
chaque segment de toiture.
Chaque groupe de quatre cylindres est alimenté par une pompe hydraulique contrôlée numériquement par automate programmable (PLC) à deux étages, de façon à pouvoir totalement maîtriser la vitesse de translation, les accélérations et les décélérations du mouvement hydraulique. L'objectif de ce système hydraulique intégré est de permettre un déplacement et un positionnement en douceur de l'arc.
Lors de l'opération de positionnement du toit, effectuée en mai et en juin, les pompes PLC étaient positionnées de chaque côté des arcs et ainsi transportées pendant toute la durée du processus. Chaque pompe fournit une pression hydraulique et une force de traction identiques aux quatre vérins pendant que la synchronisation de la course est assurée par la résistance structurelle du sabot. Les deux pompes sont conçues pour être reliées par un câble de 400 mètres et sont synchronisées par le boîtier de contrôle par automate programmable (PLC) pour pouvoir contrôler la mise en marche et l'arrêt du segment de toiture de 8500 tonnes.
L'utilisation d'un moteur AC à fréquence variable contrôlé par microprocesseur garantit des démarrages et des arrêts en douceur (tout en maintenant une vitesse acceptable). Le boîtier contrôle la vitesse du moteur électrique et donc le débit d'huile et la vitesse de rétraction des vérins de tractions.
Le boîtier de commande PLC permet de faire fluctuer la vitesse du moteur (tr/mn) linéairement, (vitesse minimale à vitesse maximale et vice versa), à l'intérieur des intervalles de temps définis par l'opérateur. Une vitesse de fonctionnement extrêmement basse est ainsi atteinte une fois le mouvement de l'arche amorcé. La vitesse est maintenue à un niveau bas pendant un certain temps, de façon à ce que le système se stabilise.
Dans un deuxième temps, le débit d'huile des pompes augmente
de façon linéaire (rampe d'accélération) pour maintenir
une accélération constante et prudente jusqu'à ce que la
vitesse de traction, telle que définie par l'équipe des concepteurs
de la toiture, soit atteinte.
Le processus de traction, le vérin enregistrant une course de vitesse constante, se poursuit. Dès que le microrupteur embarqué détecte que le piston est arrivé en fin de course, le système hydraulique s'abaisse de façon linéaire et automatique (rampe de décélération). La vitesse de rétraction du vérin est réduite à un minimum et le processus de traction est stoppé. Le processus est redémarré une fois la totalité des vérins rechargés (allongés) à grande vitesse.
Le processus est redémarré une fois la totalité des vérins rechargés (allongés) à grande vitesse.
Pour Enerpac, le projet du Stade Olympique d'Athènes illustre comment on peut intégrer l'hydraulique et l'électronique dans la création d'un système de contrôle hydraulique du mouvement et vaincre ainsi les problèmes majeurs rencontrés par les méthodes conventionnelles classiques. Grâce aux systèmes de contrôle par automate programmable, la translation hydraulique est plus facile, plus fiable et moins dangereuse.
Chaque étape du processus peut être contrôlée. Atouts
principaux du système hydraulique intégré: Comparé
aux câbles, l'emploi de longs vérins de traction à double
effet augmente considérablement la rigidité du système.
Cette application permet de réduire l'élasticité du début
de translation. Qui plus est, les vérins à double effet, électriquement
extensibles et rétractables, permettent une plus grande maîtrise
des charges lourdes en cas de forces externes imprévues (vent, inertie
causée par des arrêts brusques, etc.).
La substitution de la poussée pour la traction rend le mouvement plus
stable, élimine les risques de flambement et permet de contrôler
la longueur du vérin. Les pompes à étage double avec un
débit d'huile important permettent de réduire considérablement
le temps de recharge du vérin.
Pour de plus amples informations, contactez :
Enerpac BV
Irene Kremer
P.O. Box 269
3900 AG Veenendaal
Pays-Bas - Phone: +31 318 535911